Hi, I’m Cooper Eastwood, a rising Sophomore Aerospace Engineer focusing in Astronautics. Throughout my first year at Embry-Riddle I was given the opportunity to construct a suborbital launch vehicle alongside Gaurav Nene. My story, as well as many other Embry-Riddle students, begins long before attending college. I have been on the journey to reach space since my early days of high school and my passion has brought me very close to my goal. Through the Undergraduate Research Institute’s backing and Dr. Michael Fabian’s support we are swiftly approaching a final launch date. Our project, the Embry-Riddle Suborbital Reusable Vehicle (ERAU-SRV) is centralized around the ideas of having as little oversight as possible, a small integrated team, and to radically change the way students pursue rocketry research.
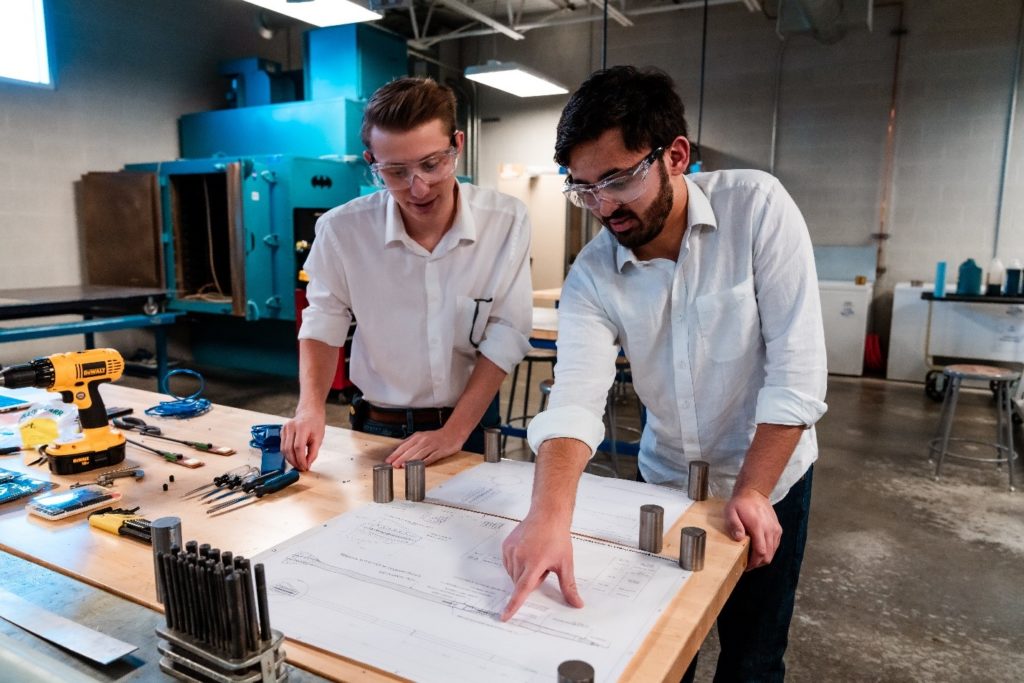
The purpose of this research is to demonstrate the use of commercial propulsion and flight systems in a fully reusable launch vehicle for reliable low-cost access to space. The rocket, standing at 11ft tall, will be a testament to a cheaper and more frequent launch strategy than comparable commercial and university developed SRVs in its altitude range. Furthermore, the gross lift off weight of the rocket is projected to be only 50 lbs. and will reach apogee at 440,000 ft and reach a maximum velocity of Mach 5, pushing the limits for university level rocketry speed, altitude, and launch rate.
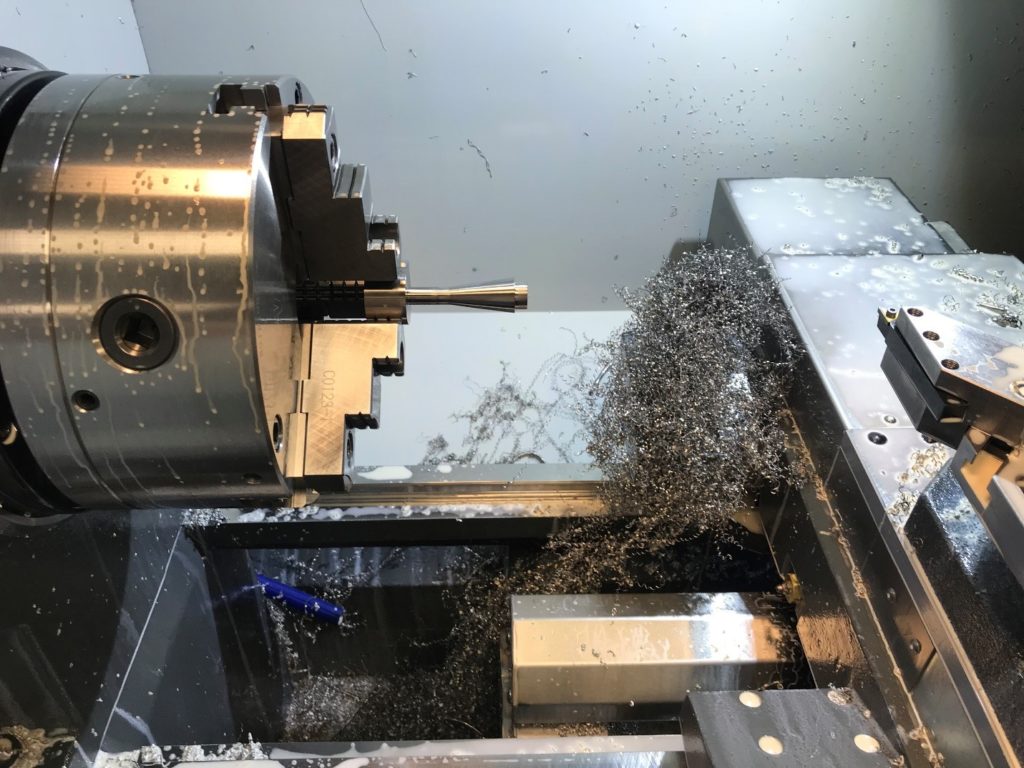
Nearing the end of the first semester the team invested weeks of testing for our onboard recovery and deployment system. This was pursued with the intention of establishing set up and take down procedures as well as a familiarity with the operations. These systems utilize barometric sensors, or atmospheric pressure sensors, to dictate velocity and ultimately deploy a parachute when the acceleration reaches zero. To test these systems in a controlled pressure environment we utilized the state-of-the-art technology in the Aerospace Experimentation and Fabrication Building (AXFAB) and the new Science, Technology, Engineering & Mathematics (STEM) building. After talking with professors and the EagleSat club, we operated the vacuum chambers located in both buildings to simulate high altitude atmospheric conditions. While referencing testing safety standards, we placed the battery and telemetric flight computer into the vacuum chambers and conducted more than thirteen tests over three weeks.
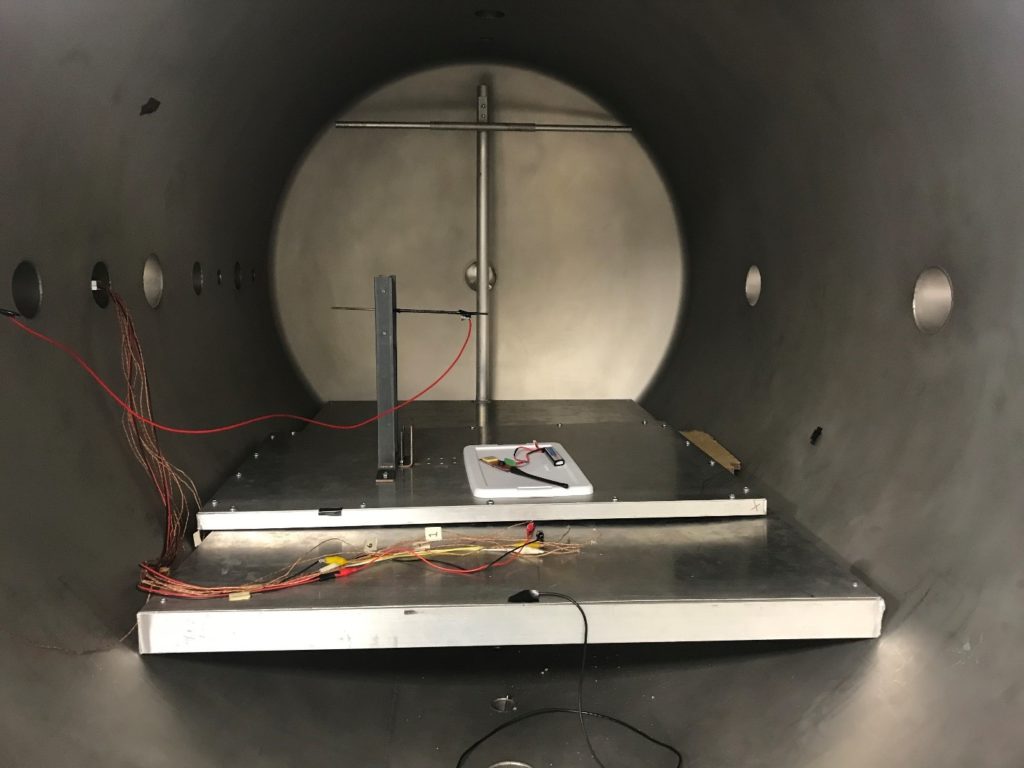
The data we gathered included: voltage outputs of two black powder ignition wires, barometric accuracy, programming and data quirks or anomalies, GPS signal lock strength and tracking, and gyroscopic orientation sensitivity. Both excited and confident with the positive testing results, I compiled our outcomes into an American Institute of Aeronautics and Astronautics (AIAA) formatted paper which was then published into their most recent journal. After the full paper’s submission, we were accepted to speak at the AIAA Region IV conference at the University of Portland and given thirty-minutes of stage time. We were looking forward to spending two days at this conference in late March and discussing our findings as well as our greater project ideas with our peers. However, this was cancelled due to COVID-19 and will be rescheduled in late 2020.
The purpose of making a procedures checklist is to cut down human error. This is especially useful for the day of launch because of anxiety, or what’s called “go fever”, can lead to detrimental mistakes. Sticking to a script and lots of practice is the best way to mitigate errors. Most corporations have entire teams dedicated to their operations; there they hammer out all the kinks in the road from construction to launch. Launch operations is vital to any rocket’s success, so we have started as early as possible to ensure a smooth launch and to maintain professionalism in the heat of the moment.
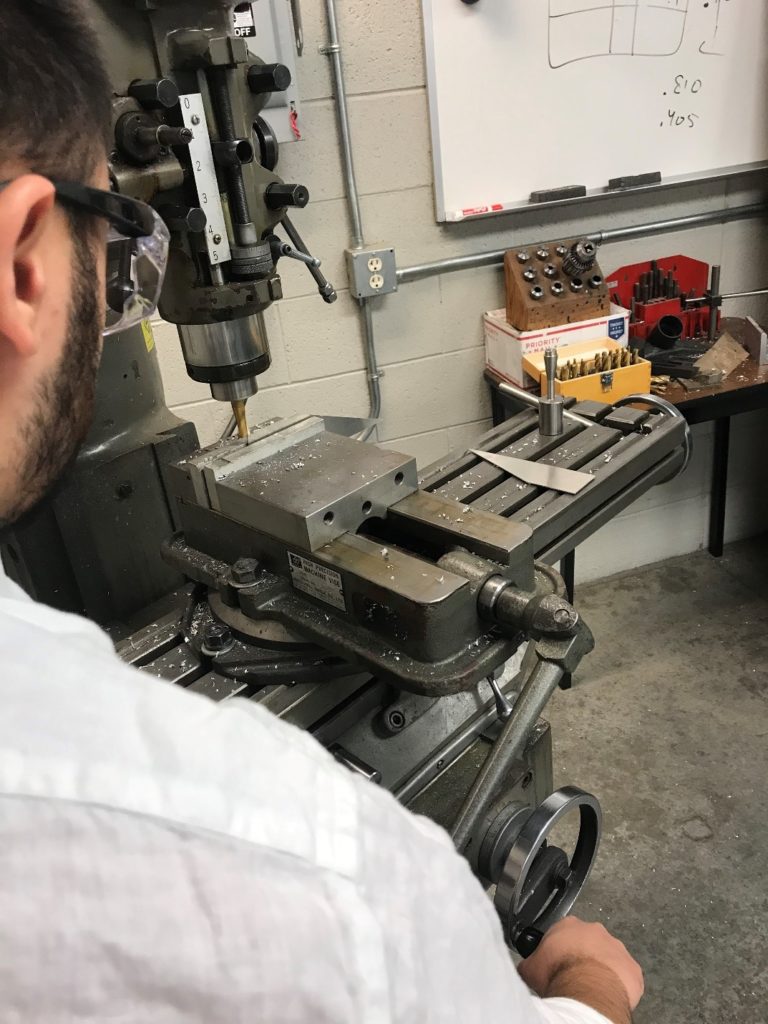
Our design had been completed in October of 2019 and we sent our manufacturing requests to AXFAB. This is where our aluminum components can be machined to AS9100 standards. Starting the beginning the second semester, we dedicated hours a day to work in AXFAB’s machine shop to help speed things along and adjust designs where necessary. Being a two-person team, we both had the knowledge and authority to request parts to be manufactured. Both us and Dr. Fabian believe in a small team approach to this work so we can easily streamline part alterations where necessary, without having to meet up and approve of every detail. With hours a day for a few months being dedicated to machine shop time we found ourselves learning tricks of the machining trade from Jared Vanetta, the machinist, in AXFAB. He has been integral in our manufacturing process as well as a mentor in our designs. The hands-on experience we got were unparalleled in any other classroom study and I found myself sitting in on a ME300 machine shop lab.
After discussions with Dr. Sensmeier and Dr. Fabian we incorporated our URI project into an official class: AE 399, a 3-credit course. It gives us an opportunity to finish the project on campus over summer while earning credit that counts toward our degrees. This was a great moment for us as our extracurricular time and effort spent was recognized by our professors and department.
The hands-on approach by professors certainly accelerated this project’s success. I find myself getting more interested in engineering every day and I hope to pursue this as a lifelong career. A note to incoming students; if you have a great idea and a goal, you can really go far with the College of Engineering’s dedication to their students and with the backing of URI.