By Cooper Eastwood
This blog is an update to Cooper’s first blog: Aiming for Space with a Fully Reusable Rocket
Hi again! I am Cooper Eastwood, an Aeronautical Engineering sophomore and co-investigator of the Embry-Riddle Suborbital Reusable Vehicle. The whole world put itself on pause and everyone felt the effects. I know that at my home in Los Angeles many businesses and everyday workers have been forced inside due to the pandemic. Online learning, commerce, and communication became the new norm. I and many others have witnessed the whole world adapt and change in only a few months. Now almost a year later much has changed but the goal is always the same: to get to space cheaper and more often.
The Embry-Riddle Suborbital Reusable Vehicle (ERAU-SRV) team transitioned completely online during the summer period. Gaurav Nene and I stayed on task even in different parts of the country through video calls and scheduled meetings. Our small integrated team dynamic allowed us an easy transition as we can continue working diligently on the next steps of development whenever necessary. During this time, we submitted the lengthy and necessary documentation for unguided commercial suborbital vehicle launch approval at Spaceport America. We coordinated documentation with the FAA’s Office of Commercial Space Transportation (AST) and the New Mexico Spaceport Authority. Then in June 2020 we received the launch approval for a future date in 2021. We are taking our two-stage launch vehicle past the Karman line, or 100 kilometers, and to do so we need to launch from an FAA licensed facility. As New Mexico begins the process of allowing more frequent travel to their federal sites, the team will be at Spaceport America to observe the launch facilities and finally meet the ground support members.
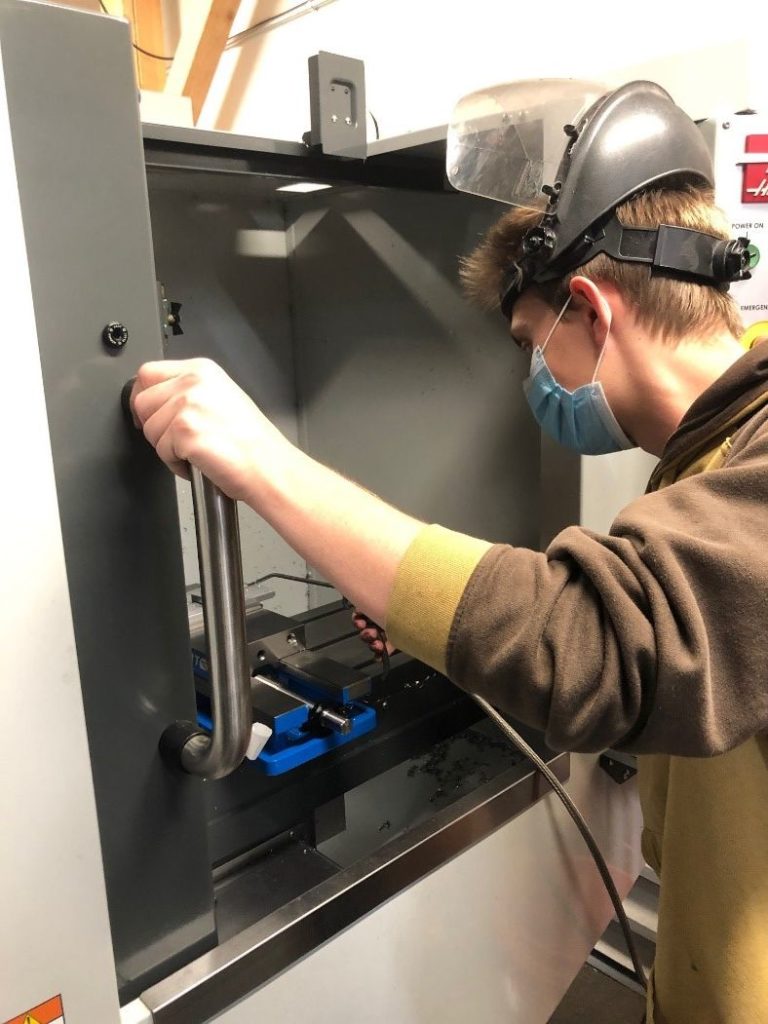
To get the final funding we needed to finish the vehicle. The College of Engineering, the Undergraduate Research Institute, and Embry-Riddle’s Daytona Beach campus opened an opportunity for student projects to win grant funding by presenting in front of the Board of Alumni. Dr. Ron Madler, Dean of the College of Engineering, extended an invitation for us to further our research and break new ground with this brand-new alumni collaboration. We submitted a proposal to the board, bidding for a chance to present. This contained our preliminary design review, our FAA package, and the AIAA published technical report regarding our avionics. We qualified as one of the top three finalists and in under a week we made our presentation. Once the dust settled, we were awarded a grant to accelerate our work! With this new thrust of momentum and enough funding to purchase the rest of the booster stage, the next step in our engineering method was to verify our vehicle.
We required a launch test of our sustainer to accomplish six objectives: verify performance and our trajectory models, qualify the structural components, validate the recovery system, validate performance of telemetry, gain experience with pre-launch operations, and gain post-launch operations experience. After five days of integration we put the vehicle on the pad at Friends of Amateur Rocketry launch site in Mojave, California.
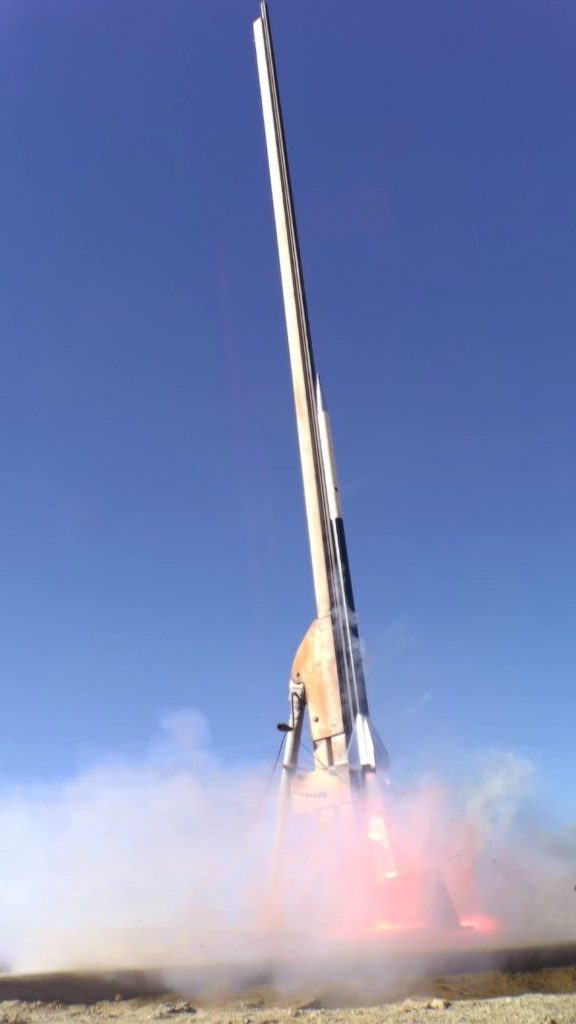
On December 19th, 2020 at around 12:30 PM, the rocket was launched and experienced a recovery system failure at apogee which was addressed in a 35-page post-flight report. The sustainer surpassed its goal of 31,666 feet – exactly 6 miles. The vehicle was only partially recovered due to ballistic reentry, however we received two sets of flight data from our identical on-board computers. Every piece of the rocket was sifted from the sand, meticulously inspected, and documented. By finishing the in-depth report we completed five of our six objectives and proved that we could take the step forward on construction of the booster stage to launch at Spaceport America.
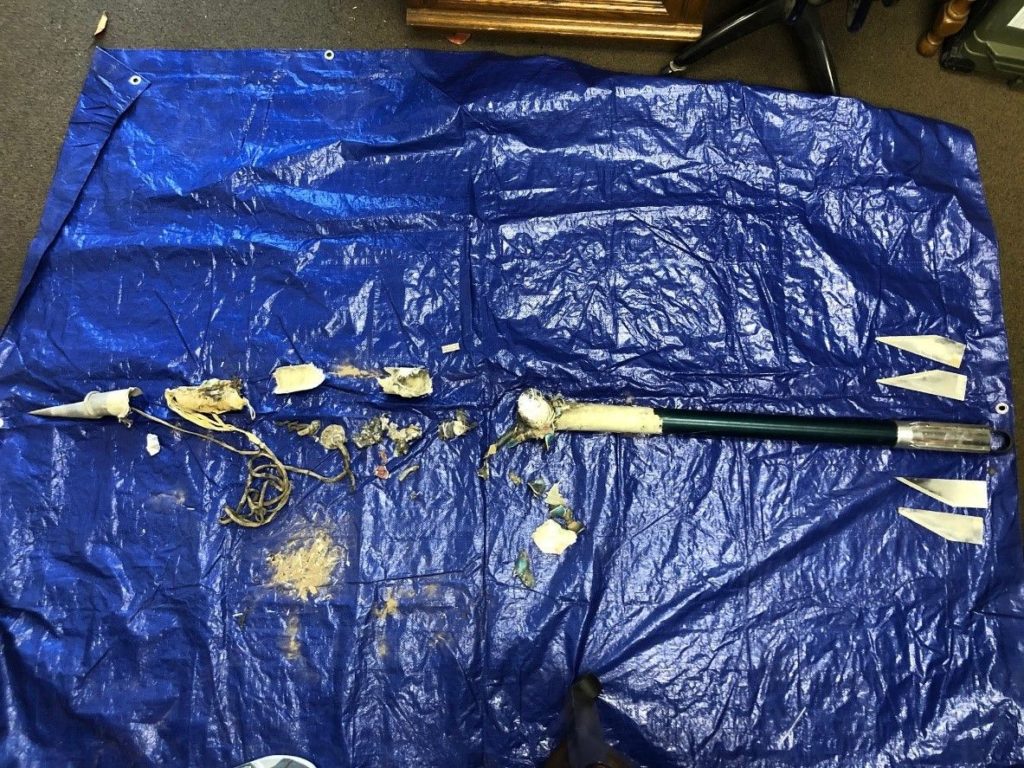
Immediately after our test we welcomed a new faculty advisor as well as a member of our team. Our previous faculty advisor Dr. Michael Fabian moved on to government research and Prof. Robert Gerrick, Mechanical Engineering Chair, took the role of our mentor. William Knoblauch, a Mechanical Engineering freshman, also became a member of our team by assisting in post-flight analysis and continuing testing research on flight critical hardware. We are in the process of accepting new members aiming to grow hands on experience with suborbital launch vehicles. As our vehicle and team grow, so do our hopes of surpassing our goals.
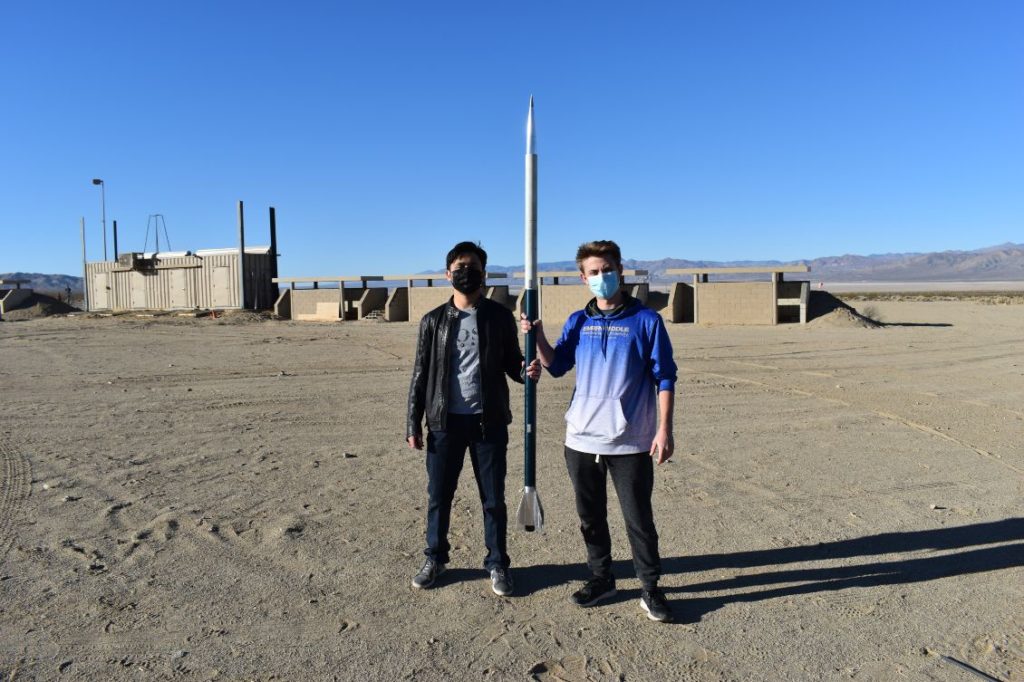
When the previous post left off, we were anticipating a trip to Portland, Oregon to attend the American Institute of Aeronautics and Astronautics (AIAA) Student Conference Region VI and present a 30-minute presentation on our avionics system at the conference. This was cancelled only a week before taking place in March 2020 and was postponed until the same time this year. Now after resubmitting the paper to a judge’s panel for review, it was accepted to the 2021 student conference at California State Long Beach and will be taking place in April.
Being a cross-discipline undergraduate research project gives us the opportunity to collaborate with a diverse group of engineers who can all contribute to space flight. As we expect many more space launches, the amount of experimental data gained per flight will be exponential. After a successful launch we will be calling on all students and as well as those considering enrolling at Embry-Riddle Prescott to form ideas, build hardware, and program experiments for the vehicle. These will all be taken to space, an environment that can be exclusively reached repeatedly only at Embry-Riddle. If you have a great idea and a goal, you really can get to space with the College of Engineering and the Undergraduate Research Institute’s backing.